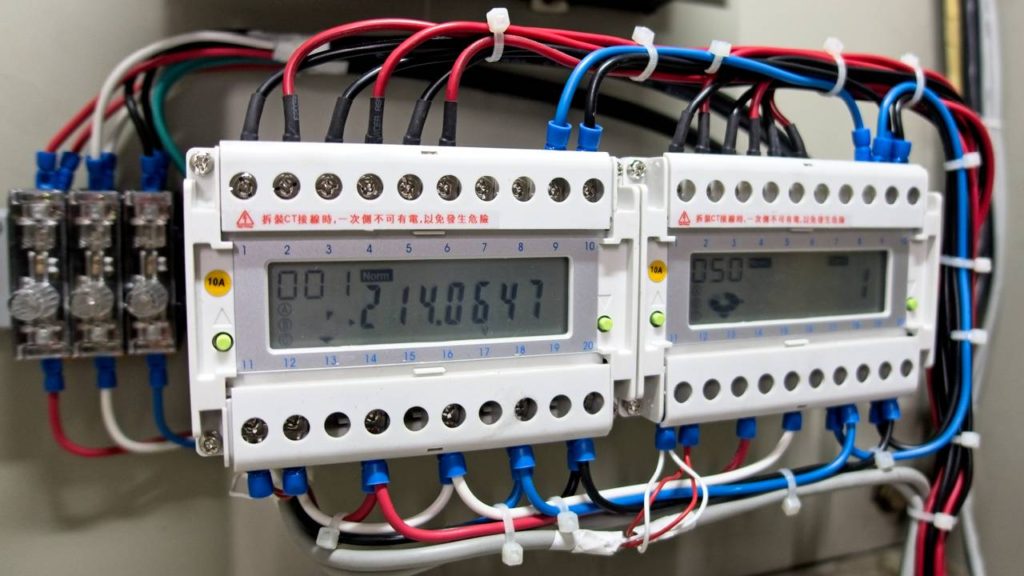
Resources consumption and reducing our reliance on it is an increasing pressure and challenge, that can never be measured in “enough”. The challenge is becoming a daily endeavour, and with Nien Hsing doing business as a vertical integrated package, the continuous struggle to find cleaner production options at all levels continues. With so many projects underway it’s easy to forget about some of the outstanding achievements of the last months and ones currently in progress.
Mills an Energy Draining Source
Textile mills just gobble up power. It’s an energy consumption monster from the first processes of carding to dyeing, weaving to various finishing applications. As such, finding ways to reduce natural resources consumption in this area has taken the forefront in our quest to look at more effective energy management for our mills.
With this, our mill division management had set out as early as 2016 on reviewing opportunities that can be implemented at the textile mill that will lead to reduction in energy consumption.

“ Energy management includes planning and operation of energy production and energy consumption units. Objectives are resource conservation, climate protection and cost savings, while the users have permanent access to the energy they need.” -- Energy Management, Wikipedia
Implementation & Success
Beginning in November 2016, the pilot for this project was launched in our Taiwan mill, Nien Hsing Textile (HouLong). The energy management system implemented was one of four identified projects to reduce natural resource energy consumption, and the purpose of the energy management project was to regulate the efficiency of air compressor automatically. Via this system, the air compressors would be activated and deactivated based on production loading, thereby cutting up easily 30% of the energy consumption on this part alone.
Another essential feature measured of the following year was the control of energy requirements between the various departments. By regularly monitoring how energy is requested and when it is done, hot spots (areas of high usage) could be identified and remediated.
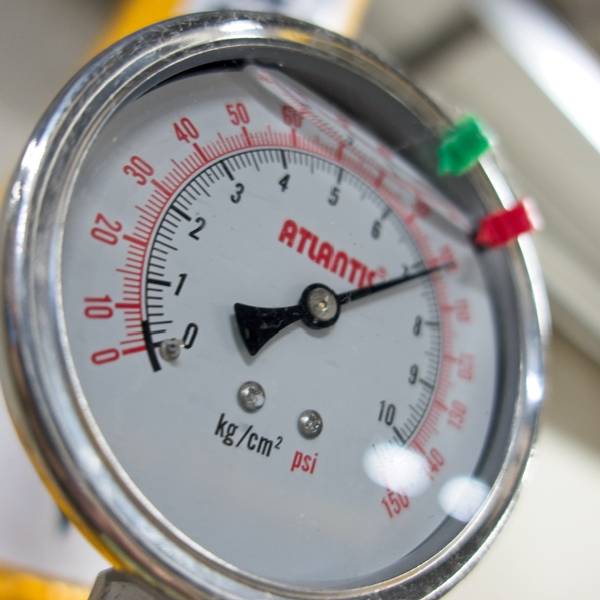

Limits can also be set, and when reached, will sound an alarm allowing the operator to investigate as to which requirements are stressing the system. This real-time feedback gives the factory full access to understand how the production is taxing on various energy processes.
Expansion
Based on the successes obtained by our Taiwan mill facility, the management system is now under investigation for other regions and partnerships that will bring these benefits to all the mills.
Additional investigations are also launched into how much such a system can benefit garment facilities – though less intensive in their demand for high loading of electricity – still rely heavily on natural energy resource consumption.